Laminate pressing machines – also known as panel presses or veneer presses – are precision-engineered woodworking press machines essential for bonding decorative surfaces (laminates, veneers or finish foils) onto core panels (MDF, plywood, particleboard, honeycomb, etc.).
These heavy-duty hydraulic presses deliver uniform pressure (often hundreds to thousands of tons) and, in the case of hot presses, precise heat, to ensure strong, durable bonds.
Industries from furniture to flooring rely on these industrial panel presses to produce high-quality laminated panels with unmatched durability and high-output efficiency.
Leading brands like Italpresse (Italy), Ormamacchine (Italy) and JoosUSA (USA) have long set the standard with robust hydraulic designs. Bestin’s range of laminate presses follows suit – offering industry-trusted, tailor-made solutions that deliver precision, speed and reliability to modern production lines.
This article will explore this machine.
Featured Resource
Table of Contents
1. How the Lamination Process Works
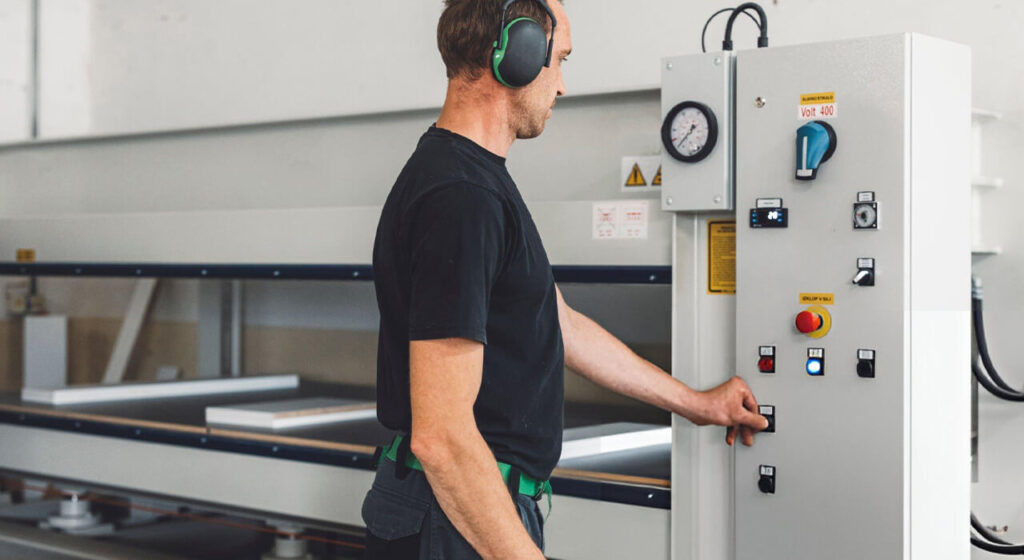
Laminating wood panels involves a sequence of careful steps:
-
Glue Application: First, an adhesive is spread evenly on the wood substrate or laminate sheet. This is done with a roller or spreader to ensure uniform coverage. The glue type depends on the process: cold presses use fast-setting PVA wood glues, while hot presses use melamine, phenolic or other heat-activated resins.
-
Stacking Layers: The decorative laminate (paper, film or veneer) is aligned on the glued surface. If multiple layers are needed (e.g. core veneers for plywood), each layer is stacked accordingly. Protective sheets may be placed between layers when pressing plastic films.
-
Pressing: The assembled stack is loaded into the laminating press. In a hot press, the platens are pre-heated (often up to ~300°C) before descending on the panel. In a cold press, room-temperature platens compress the stack. Powerful hydraulic cylinders then apply even pressure across the board. For example, a cold-press system uses an adhesive spreader and an “Air Pod” platen that holds the entire stack under constant pressure while the glue cures.
-
Curing: Under pressure (and heat if applicable), the adhesive sets and bonds the layers. The press holds the panel for the programmed cycle time. Hot presses can cure the adhesive in just a few minutes, thanks to heat acceleration, while cold presses often hold panels for many minutes to allow glue to set.
-
Unloading and Finishing: Once the cycle completes, pressure is released and the panel is removed. The laminated panel is then trimmed and allowed to cool or cure fully. The result is a strong, uniform composite panel. In many cases, the laminated panel ends up stronger than solid wood. Modern presses often include programmable pressure and temperature controls to ensure consistent results every cycle.
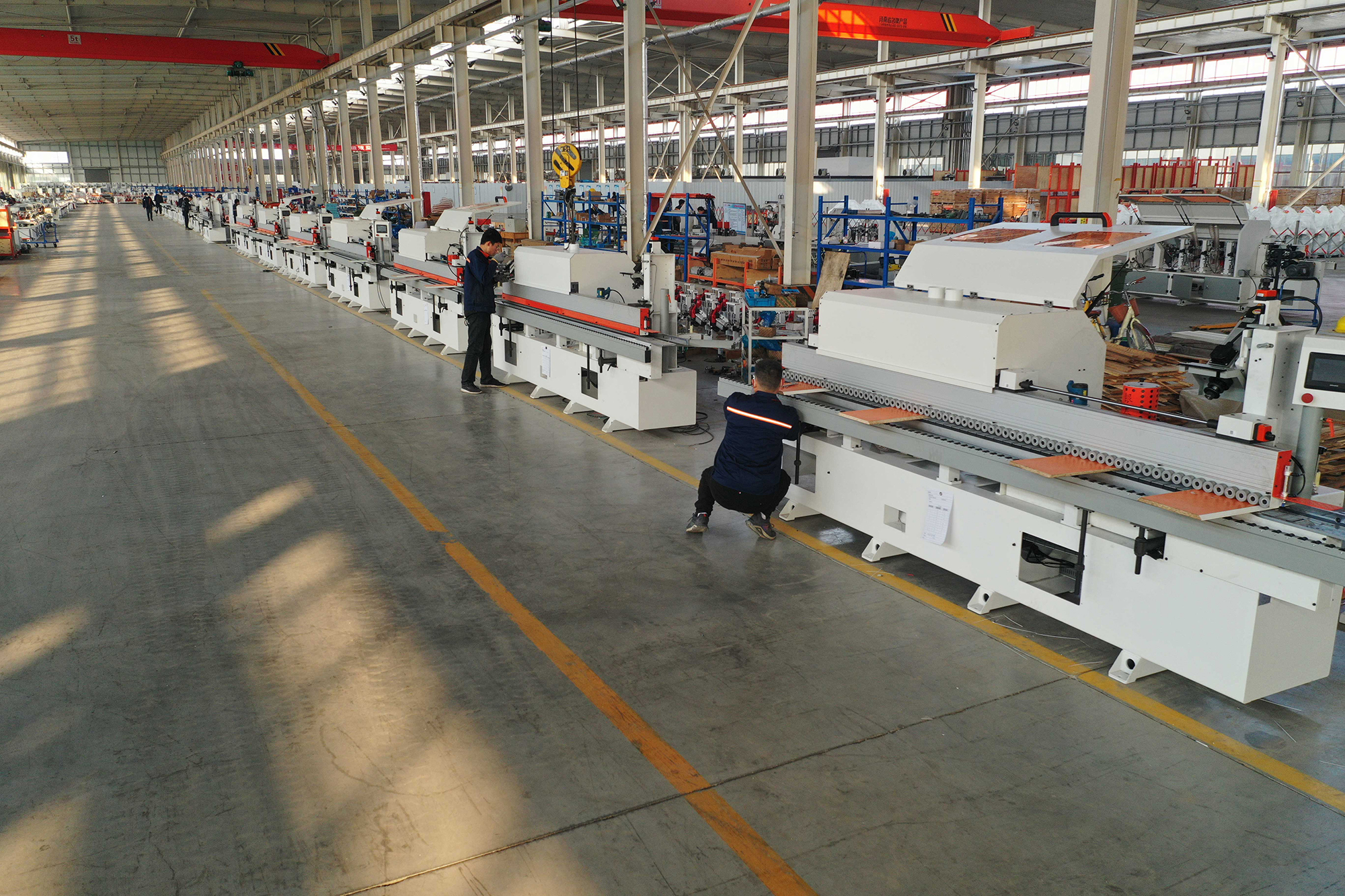
2. How the Lamination Process Works?
Laminate pressing machines fall into two main types: hot presses and cold presses. The choice between them depends on your application, materials and production priorities.
2.1. Hot Press Machine (Hot Laminate Press)
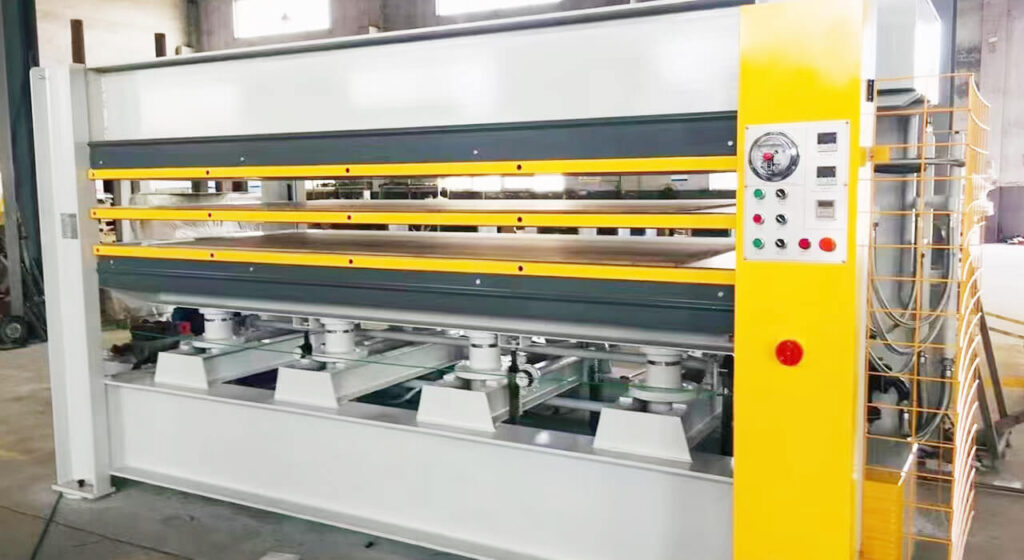
Uses heated platens (typically 100–120 °C) to cure thermosetting adhesives (e.g. melamine resin). Heat accelerates glue cure and improves bond strength, yielding very high production throughput.
For example, hot pressing can bond a 19 mm board in roughly 7–11 minutes. Modern multi-daylight hot press lines even allow continuous loading of panels, making them ideal for high-volume operations.
Hot presses excel at applying high-pressure lamination of HPL/melamine onto MDF, plywood or particleboard – common in cabinetry, flooring and countertop manufacturing. The main advantage is high-output efficiency and strong bond quality, while the drawback is the energy cost and potential internal stress from heat.
2.2. Cold Press Machine (Cold Laminate Press)
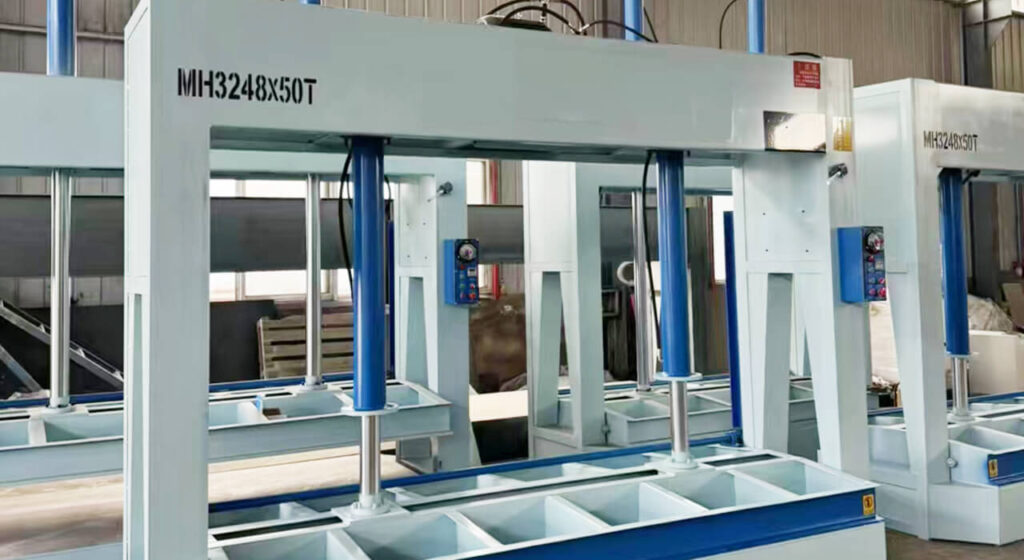
Operates at room temperature, relying solely on pressure. Advanced cold-curing adhesives (PU, EVA, etc.) bond the layers over a longer cycle.
Cold pressing often involves stacking panels in a multi-layer press. This process yields superior panel quality for certain applications, with minimal internal stresses and deformation.
In fact, Ormamacchine notes that “the cold process grants…a finished product having better characteristics than those which can be obtained by hot pressing”.
Cold presses are popular in the furniture industry for veneering MDF or particleboard panels, doors and cabinet faces.
The trade-off is longer curing times – often hours (e.g. 6–8 hours for a full bond) – which slows throughput. New fast-curing adhesives have narrowed this gap, but cold presses remain lower-speed compared to hot presses.
2.3. Hot Press Vs. Cold Press
The table below summarizes the key differences between hot and cold laminate presses:
Feature |
Hot Press |
Cold Press |
Heat |
Heated platens (typically 100–120 °C) |
Ambient temperature (no external heat) |
Pressure |
Hydraulic cylinders (0.6–1.2 MPa typical) |
Hydraulic cylinders (often higher pressure, e.g. 1.2 MPa for UF glue) |
Glue |
Minutes per panel (e.g. ~7–11 min for 19 mm thickness) |
Hours (often 6–8 hours full cure) |
Throughput |
Very high (multi-daylight lines, continuous loading) |
Lower (batch stacking; limited by adhesive cure) |
Applications |
Bonding HPL/melamine to MDF/HDF/chipboard; plywood lamination; thick laminates |
Veneering and laminating furniture panels (doors, cabinets); small batches of |
Advantages |
Fast cycle, high production efficiency, strong bonds |
Minimal board stress/deformation, excellent surface finish |
Disadvantages |
Energy-intensive; potential heat-induced stress |
Long cure cycles; requires pressing time and stack handling |
Common |
Heated hydraulic laminate press |
Stacking or platen cold laminate press |
3. Choosing the Right Laminate Press Machine
Choosing the right press depends on your production needs. Key considerations include:
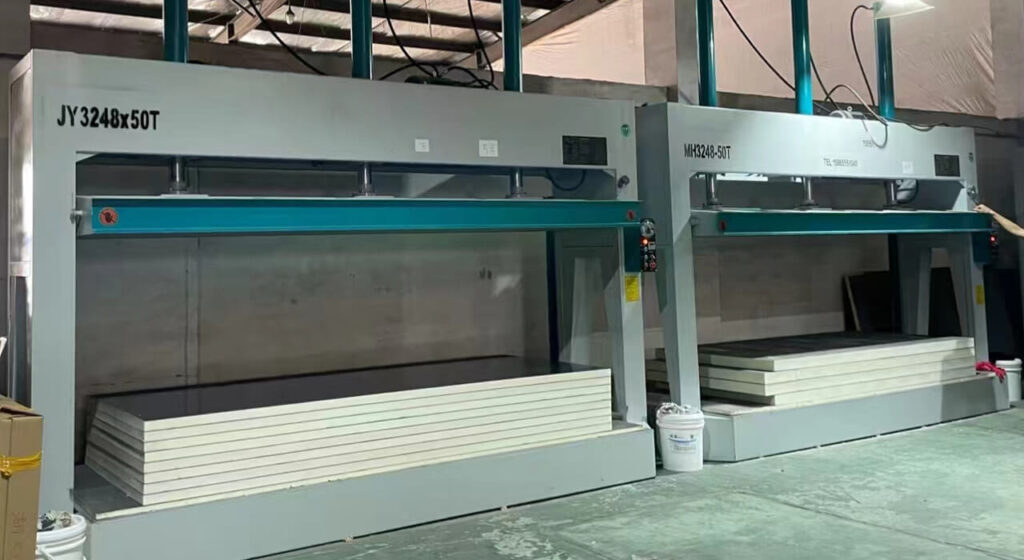
3.1. Production Volume
High-volume plants often need industrial-scale presses (e.g. large automated hot-press lines or multi-frame cold presses). Smaller shops may use bench-top or two-platen presses that fit batch production.
3.2. Materials and Finish
Identify your substrate and laminate types. If your materials are heat-sensitive (certain plastics or veneers) or you need to preserve wood appearance, use a cold press or vacuum laminator. For waterproof or heavy-duty laminations (marine plywood, exterior panels), a hot press with the right resin is usually required.
3.3. Panel Size & Thickness
Ensure platen dimensions match your largest panels; many hot presses offer multi-daylight or large single-daylight formats. Cold presses can stack multiple smaller panels simultaneously, increasing efficiency in small-panel production.
3.4. Maintenance and Safety
Safety features like emergency stops, light curtains and two-hand controls are essential for any high-force press. Regular maintenance (hydraulic oil changes, cleaning, inspections) keeps the press running smoothly. As one industry guide notes, treat a press as a long-term investment – proper care will keep it safe and reliable
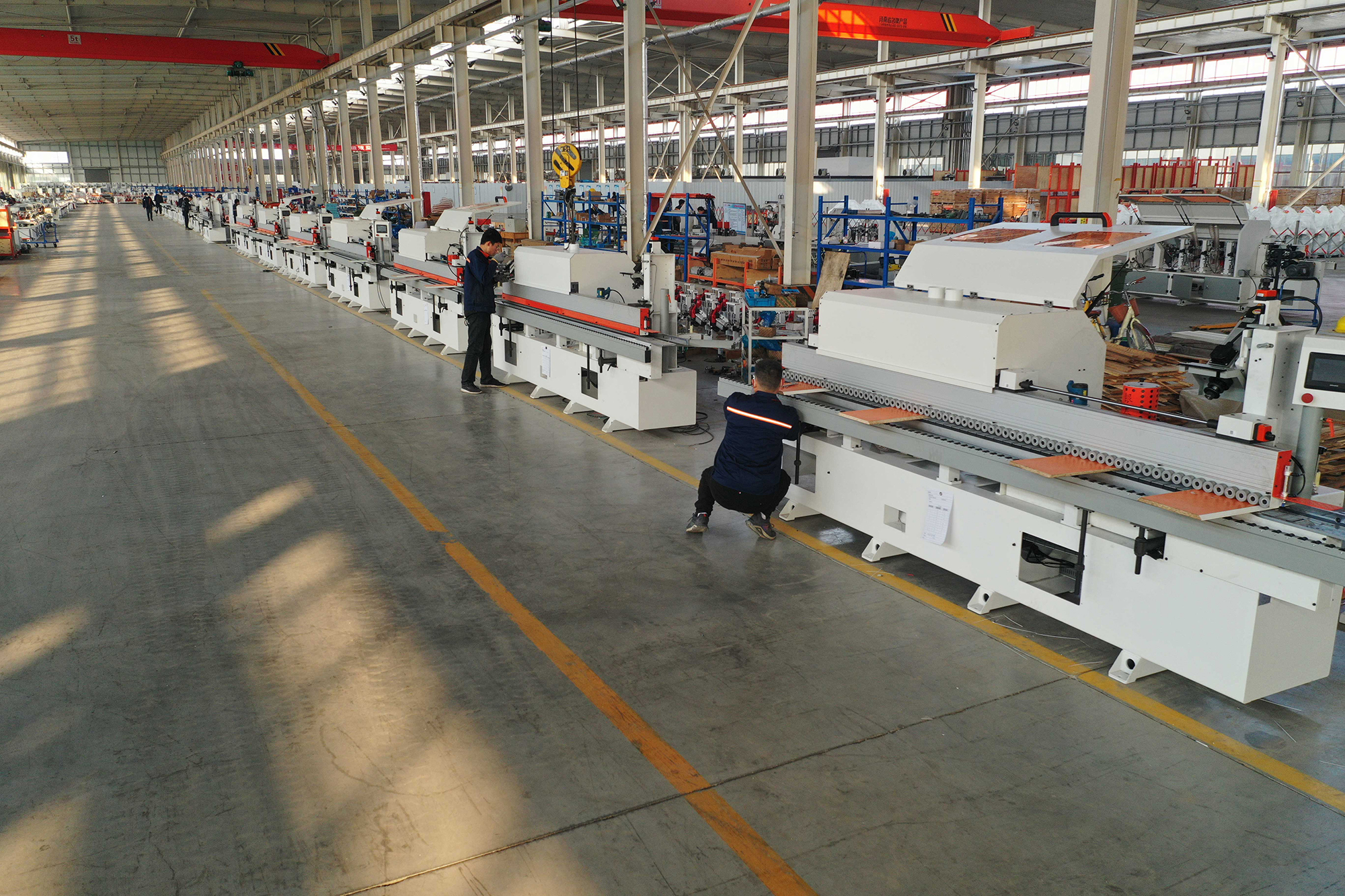
4. Bestin Laminate Press Machines
Choosing the right press depends on your production needs. Key considerations include:
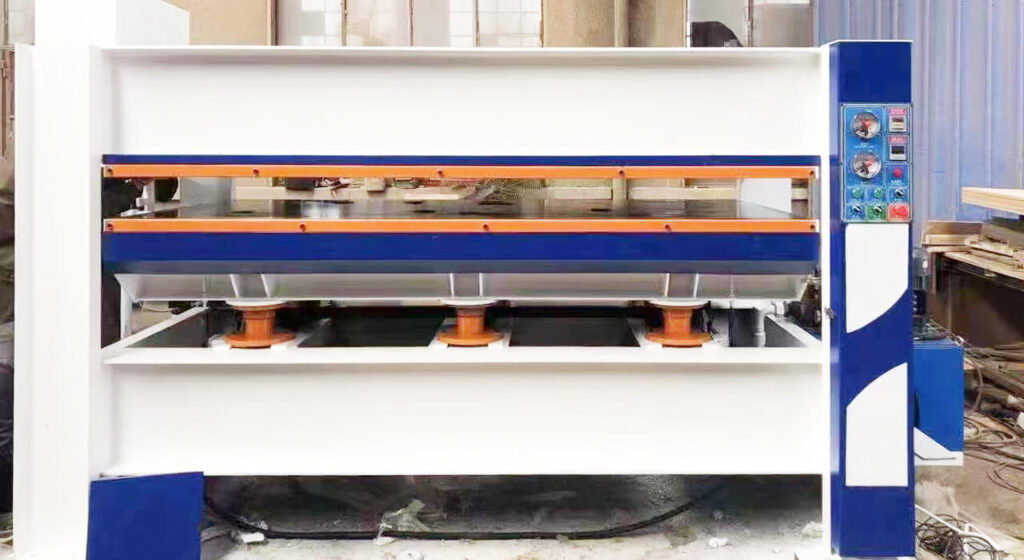
Bestin offers a comprehensive line of precision-engineered hydraulic laminate press machines designed for demanding industrial use. Every Bestin press is tailored to your production line, with platen sizes, tonnage and automation customized for your products. Key features include:
-
Precision Hydraulic Design: Advanced dual-stage pumps and PLC controls ensure uniform pressure distribution and consistent lamination every cycle.
-
High-Output Efficiency: Robust drive systems and fast platen heating (for hot presses) minimize cycle times. Bestin presses deliver high-output efficiency, maximizing throughput while maintaining bond quality.
-
Unmatched Durability: Welded steel frames and heavy-duty components provide rugged reliability. Bestin machines are built for continuous industrial use, promising a long service life with minimal maintenance.
-
Industry-Trusted Quality: Like leading brands such as Ormamacchine and Italpresse, Bestin prioritizes quality control and innovation. All machines meet CE and ISO standards, reflecting Bestin’s commitment to performance and safety.
-
Versatile Applications: Bestin’s hot presses handle HPL/melamine laminations on MDF and plywood, while its cold presses work perfectly for veneering and overlaying decorative panels. Our presses even accommodate advanced materials (e.g. wood composites, honeycomb cores) used in specialty panel and furniture fabrication.
-
Customized Automation: Choose from semi-automatic or fully automatic lines (including conveyor loading, frame manipulators, cooling conveyors, etc.) to integrate with your existing workflow. Bestin can also supply glue spreaders and membrane presses to complete your laminating solution.
If you need a furniture laminating machine or industrial panel press that’s built for precision and productivity, Bestin has you covered. Our team will help you select or customize a press that fits your wood types, panel sizes, and production goals.
Below is a quick comparison of hot versus cold presses to help guide your decision:
Feature |
Hot Press Machines |
Cold Press Machines |
Heat Source |
Heated platens (e.g. electric, hot water
or oil) – up to ~120 °C |
Ambient temperature (no external heat) |
Glue Type |
Thermosetting resins (melamine, phenolic,
etc.) |
Cold-curing adhesives (PU, EVA, casein,
PVA, etc.) |
Cure Time |
Fast cure – often only minutes (e.g.
50–60 s per mm for veneer) |
Slow cure – typically hours (e.g. 6–8
hours full bond) |
Production Rate |
Very high (multi-daylight lines with
conveyors) |
Lower (panel stacks pressed in batches) |
Suitable Applications |
Bonding HPL/melamine to MDF/HDF; plywood
laminates; thick decorative panels |
Veneering or laminating furniture panels,
doors, tabletops; delicate finishes |
Advantages |
High-output efficiency and strong bonds;
shorter production cycles |
Minimal internal stress and warpage;
better finish on sensitive veneers |
Disadvantages |
Higher energy use and heating time;
potential stress on wood |
Long cycle times; requires curing time
and backing plates for uniformity |
Industry Example |
Italpresse and JoosUSA specialize in hot
press lines for laminating |
Ormamacchine and Allwood promote cold
presses for furniture laminating (stacked veneers) |
5. Conclusion
Laminate pressing machines are the cornerstone of high-quality wood panel production. By understanding the differences between hot presses and cold presses – and matching the machine type to your materials, volume and finish requirements – you can achieve precision bonding and superior panel strength.
Ready to upgrade your laminating capabilities? Contact Us today to compare models, request a custom quote.
Our engineers will help you choose the most efficient, cost-effective laminating solution for your needs.