In industrial and commercial woodworking, the choice of cutting equipment profoundly affects product quality, productivity, and cost. Precision is paramount – accurate cuts reduce waste and ensure components fit together seamlessly.
Plywood cutting machines have evolved to meet high-volume and high-precision demands, from small cabinet shops to large factories.
Selecting the right machine type – whether a panel saw, CNC router, or laser cutter – can significantly improve efficiency and return on investment.
This guide reviews each machine, compares their capabilities, and maintenance factors to help industry professionals make an informed decision.
Featured Resource
1. Types of Plywood Cutting Machines
Industrial woodworking shops typically use several main machine types for cutting plywood. Each has distinct capabilities:
1.1. Panel Saws (Sliding Table Saws)
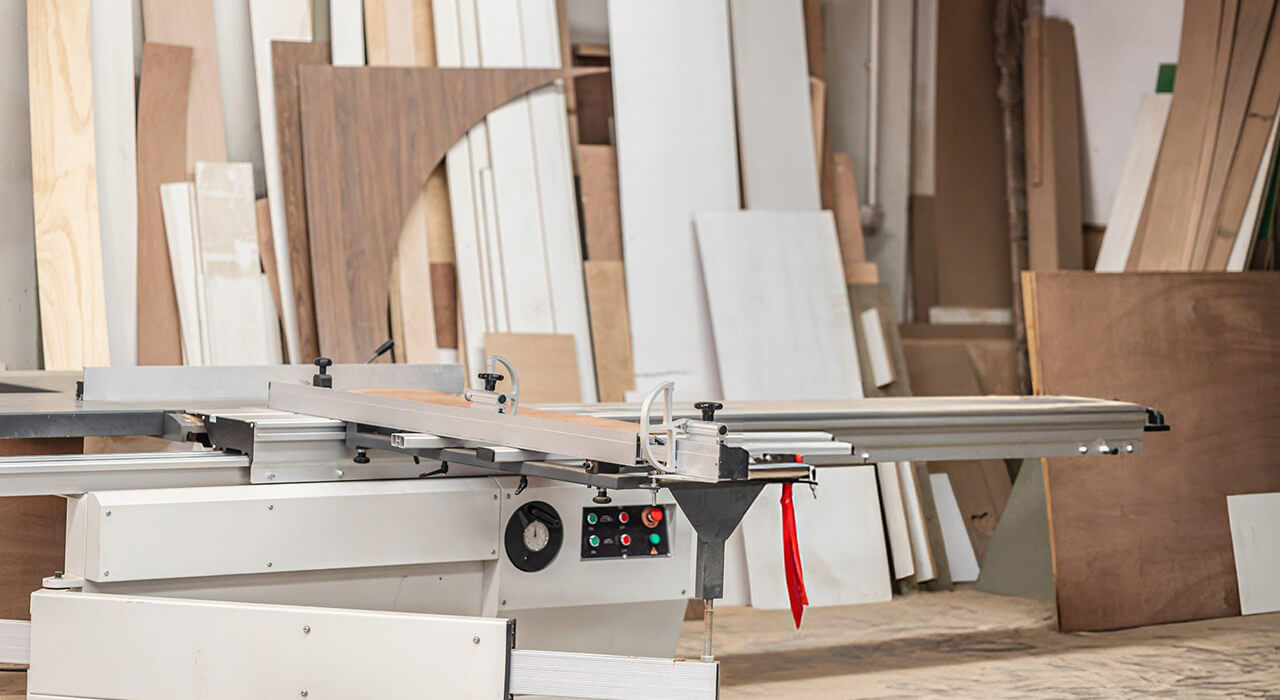
These are the workhorses for breaking down large plywood sheets into smaller panels.
A sliding-table panel saw has a large moving table and a powerful main blade. Vertical versions save floor space, making them suitable for small shops, while horizontal (beam) saws offer the highest accuracy and throughput for big operations.
High-end panel saws can even cut thick stacks (up to 50–120 mm) in one pass with kilowatt-level motors. (The photo below shows an industrial beam saw designed for high-speed panel cutting.)
Panel saws are the workhorses of high-volume plywood cutting. They use powerful motors and rigid frames to cut large stacks of material with precision. Vertical panel saws save shop space, while horizontal sliding-table saws deliver superior accuracy for large-format cutting.
1.2. CNC Routers/Nesting Machine
CNC routers/Nesting Machineuse a rotating cutting head to plunge, cut, and shape plywood.
These machines provide “the highest level of precision and automation”. They excel at cutting intricate shapes, customized profiles, and nested parts.
With heavy gantries and servo drives, CNC routers/nesting machine can hold tolerances of 0.1–0.5 mm over large areas. Many CNC routers/nesting machine have multiple heads or tools for drilling, grooving, and cutting in one setup.
They are ideal for complex furniture panels, cabinetry, and high-mix production.
1.3. Laser Cutters
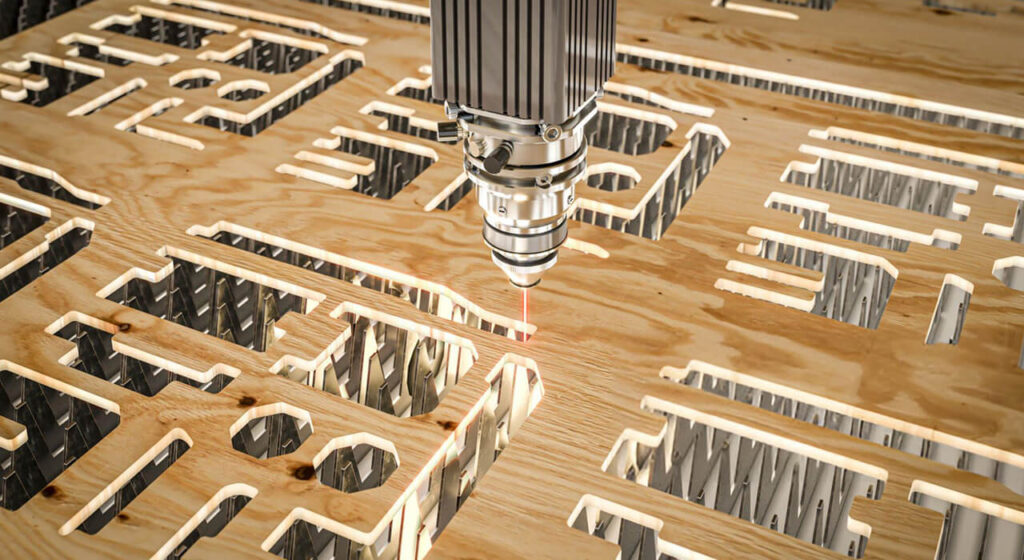
CO₂ laser cutters direct a focused light beam onto the plywood, vaporizing material. This non-contact cutting yields extremely smooth, chip-free edges, and can easily replicate detailed designs and engravings.
Lasers are “known for their precision” and are ideal for fine detail work.
However, laser beams have limited power penetration: thin plywood (3–6 mm) cuts quickly, but very thick panels may require multiple passes or are not feasible. (Also, only certain plywood grades are safe for lasers: Class I interior plywood works well, whereas exterior-grade plywood (Classes II/III) contains adhesives that can emit toxic fumes when lasered.)
Laser cutters excel at detail. The photo below illustrates a laser-cut plywood panel with a finely engraved design. Lasers produce perfectly smooth edges and even lightly “seal” the cut face due to the burning action. Because the beam is very thin, laser cutting wastes minimal material.
However, lasers require specialized ventilation (to remove fumes) and are typically more expensive than mechanical saws. They also cannot cut certain materials (e.g. PVC) and struggle with very thick plywood.
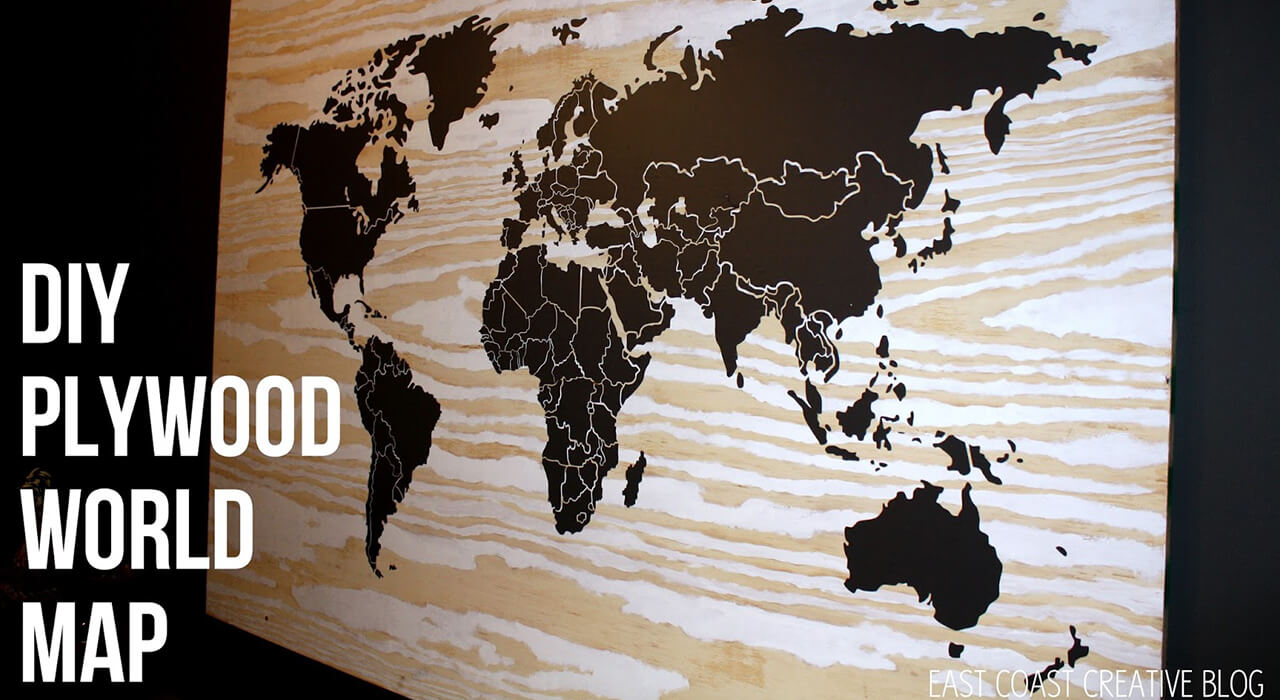
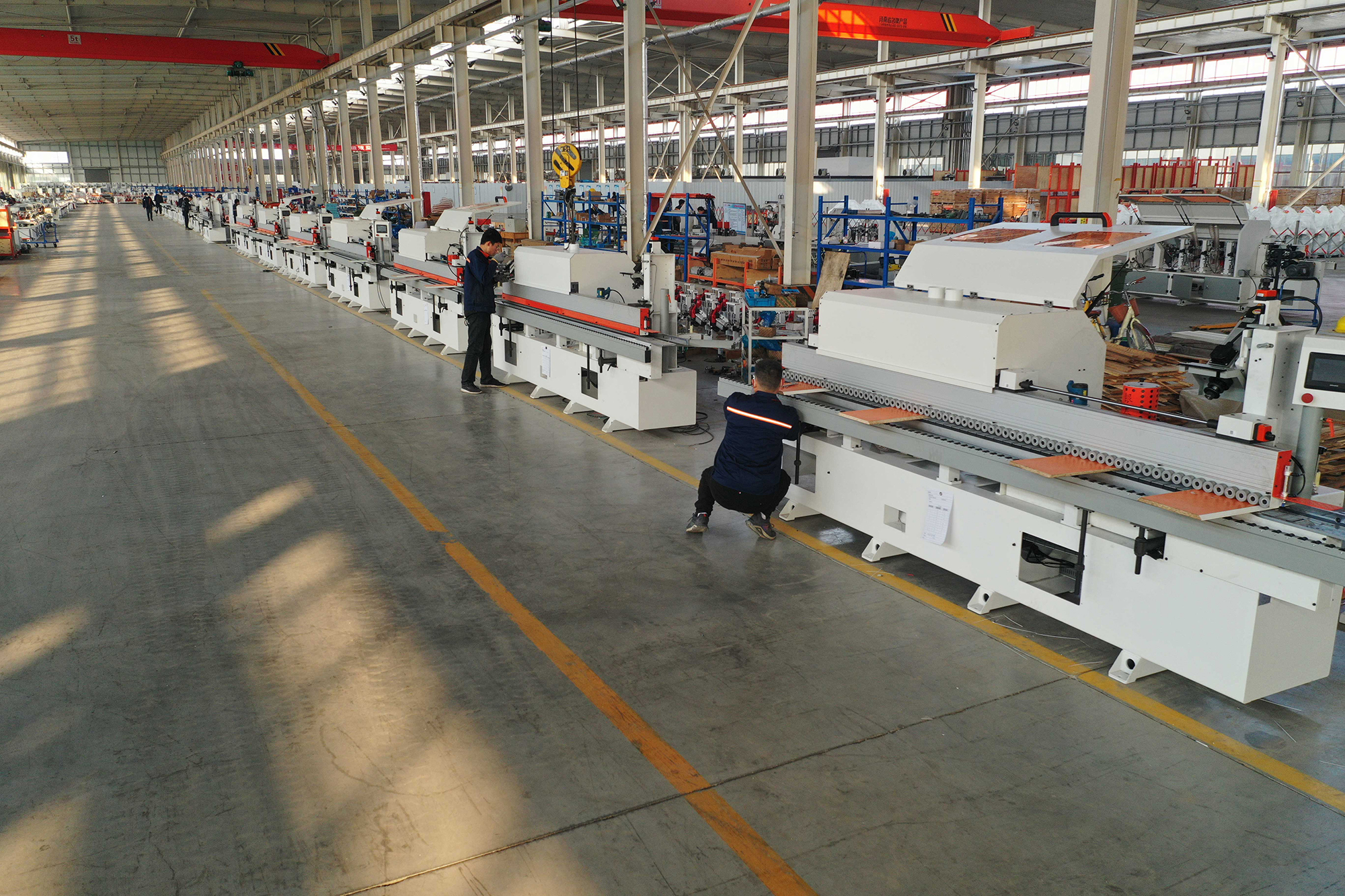
2. Key Selection Factors
When evaluating a plywood cutting machine, keep these critical factors in mind:
2.1. Cutting Capacity (Size & Thickness)
Ensure the machine can handle your plywood sizes and thicknesses.
Industrial panel saws often accommodate full 4×8′ (1220×2440 mm) sheets and thick panels (up to 80+ mm in a single pass).
Desktop machines or small CNCs may limit sheet size. Check the maximum cut length, width and height specifications.
Also consider the thickness range: lasers and small saws excel on thin sheets (3–6 mm), whereas heavy panel saws and CNC routers can take 12–30 mm or more.
2.2. Precision and Accuracy
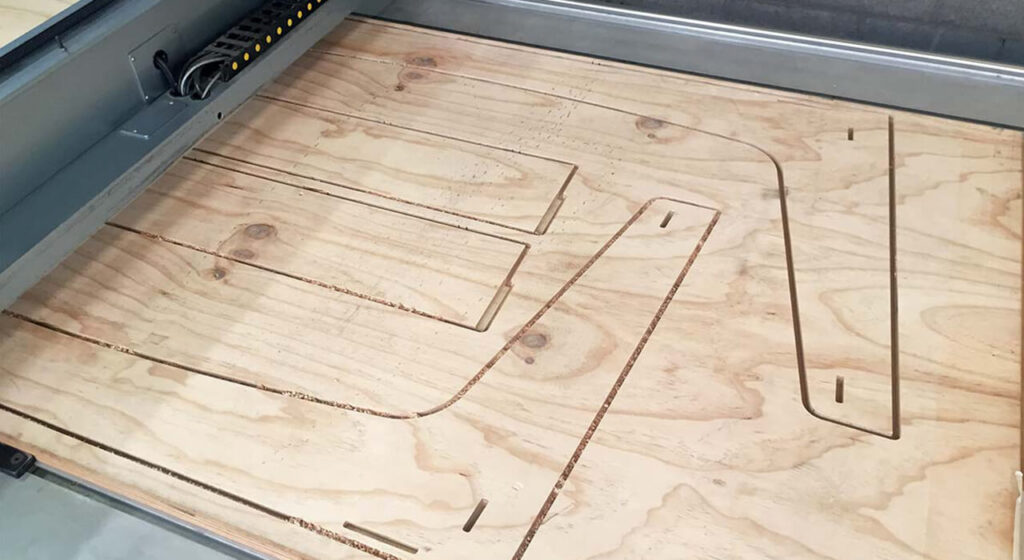
Look for machines with tight tolerances. High-end CNC router and lasers can maintain accuracy down to 0.03–0.1 mm. Mechanical saws’ precision depends on table alignment, blade quality, and fences.
Verify the manufacturer’s stated cut tolerance and repeatability. Machines with digital control and fine adjustment knobs help achieve consistent fits in cabinetry and furniture.
2.3. Material Compatibility
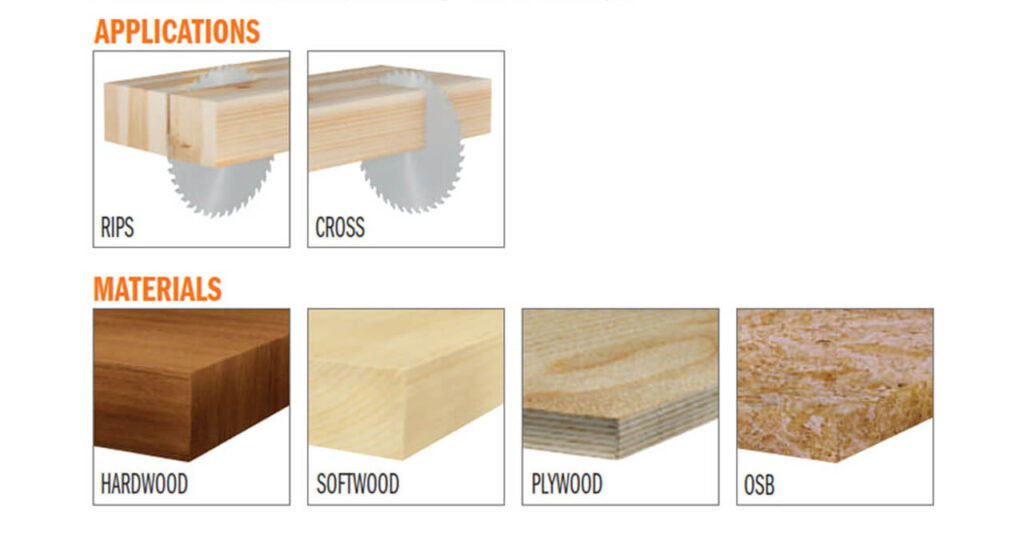
Make sure the machine works with the wood species and plywood grades you use. All machines will cut standard hardwood or softwood plywood, but only lasers can also engrave non-wood materials (acrylic, fabrics, etc.).
Conversely, lasers struggle with plywood containing certain adhesives.
For example, Virmer warns that only Class I (indoor-grade) plywood is safe for laser cutting; exterior plywood (Class II/III) has phenolic resins that “can emit toxic substances” under heat.
Check that your machine (spindle, blade, or beam) is rated for the types of plywood (hardwood veneer, composite, MDF, etc.) you plan to process.
2.4. Automation and Control
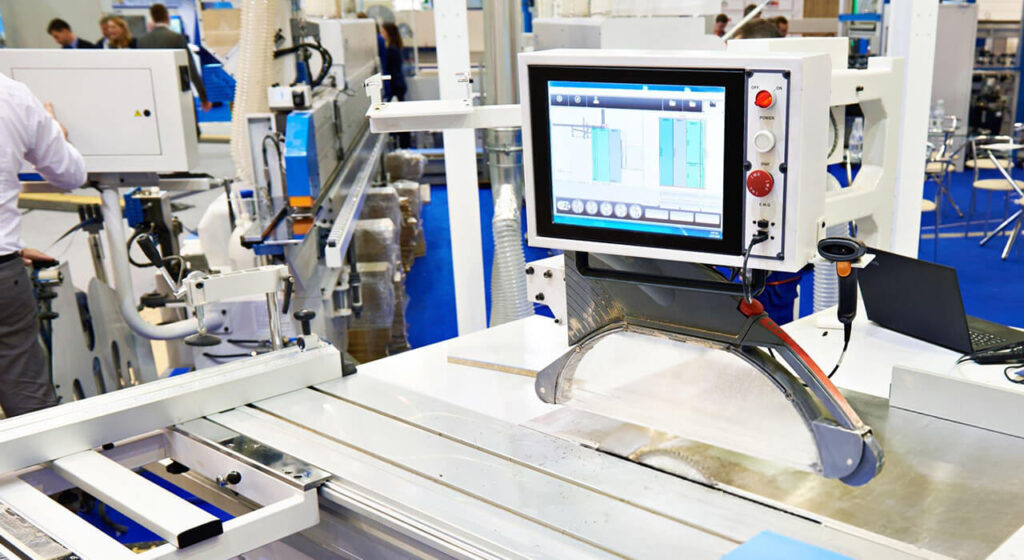
Consider the level of CNC or software integration. Basic panel saws are semi-manual, while advanced CNC routers come with nesting software and full CNC control.
Laser cutters also use CNC motion. Automated material handling (like conveyors or robotic loaders) can improve throughput.
Evaluate ease of programming: some systems use proprietary software, while others accept common formats (DXF, etc.). Good control systems and user interfaces reduce training time and errors.
2.5. Safety Features
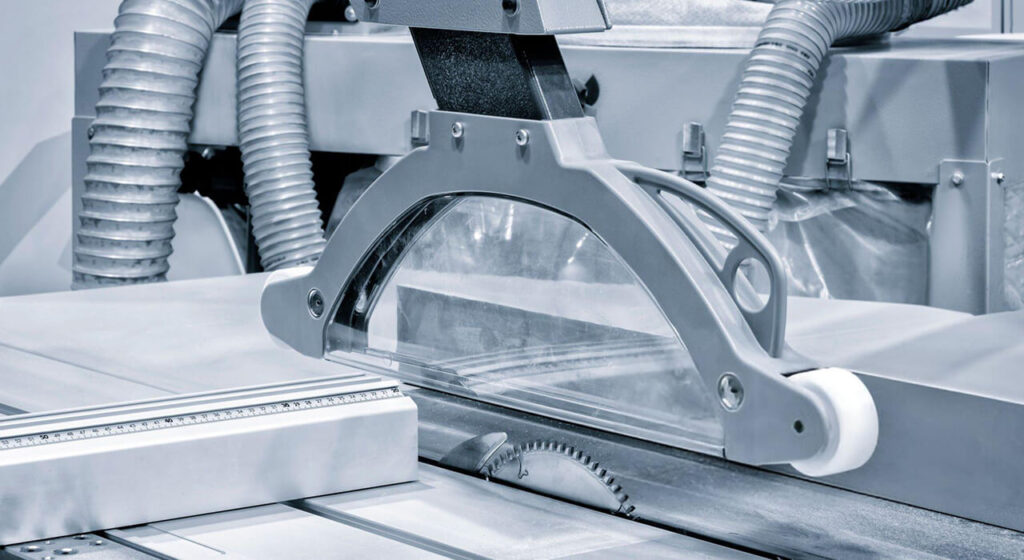
Protecting operators is essential. Key features include blade guards, emergency-stop buttons, and integral dust collection.
Panel and table saws often have mechanical blade covers and anti-kickback pawls.
CNC and laser machines should have enclosed cutting areas or light curtains to prevent injury. Wigwamply emphasizes essentials like “blade guards” and an “easily accessible emergency stop”.
Also look for dust extraction systems, especially for sawing and routing, to keep sawdust out of the workspace and protect health.
3. Comparing Popular Machines
The table below highlights a few well-known industrial plywood cutting machines and their key features:
Machine (Type) |
Highlights / Ideal Use |
Precision sliding panel saw. Known for exceptional accuracy and ease-of-use, it handles large plywood sheets smoothly. Automatic cutting programs and fine adjustments make it ideal for furniture shops that cut many full-size panels. |
|
High-end CNC routing center. Delivers “exceptional CNC capabilities” and is tailored for intricate, complex shapes. It can cut a wide range of plywood thicknesses and patterns. Advanced software and automation features suit high-volume panel nesting in cabinetry factories. |
|
Cabinet-style table saw with active safety. It provides excellent precision for crosscuts and rip cuts, and features the famous blade-stopping safety system that halts the blade on skin contact. Best for shops prioritizing operator safety on straight-cut tasks. |
|
Versatile mid-range CNC. Offers large cutting area with robust construction. Users praise its high accuracy and user-friendly controls. It cuts large plywood sheets efficiently and is a reliable choice for both custom shops and light production environments. |
These examples illustrate the range of options. When comparing models, note their cutting capacity (sheet size), automation level, and specialty features (e.g. automatic blade change, multiple cutting heads, etc.). Always match the machine’s strengths to your production needs (see “Key Factors” above).
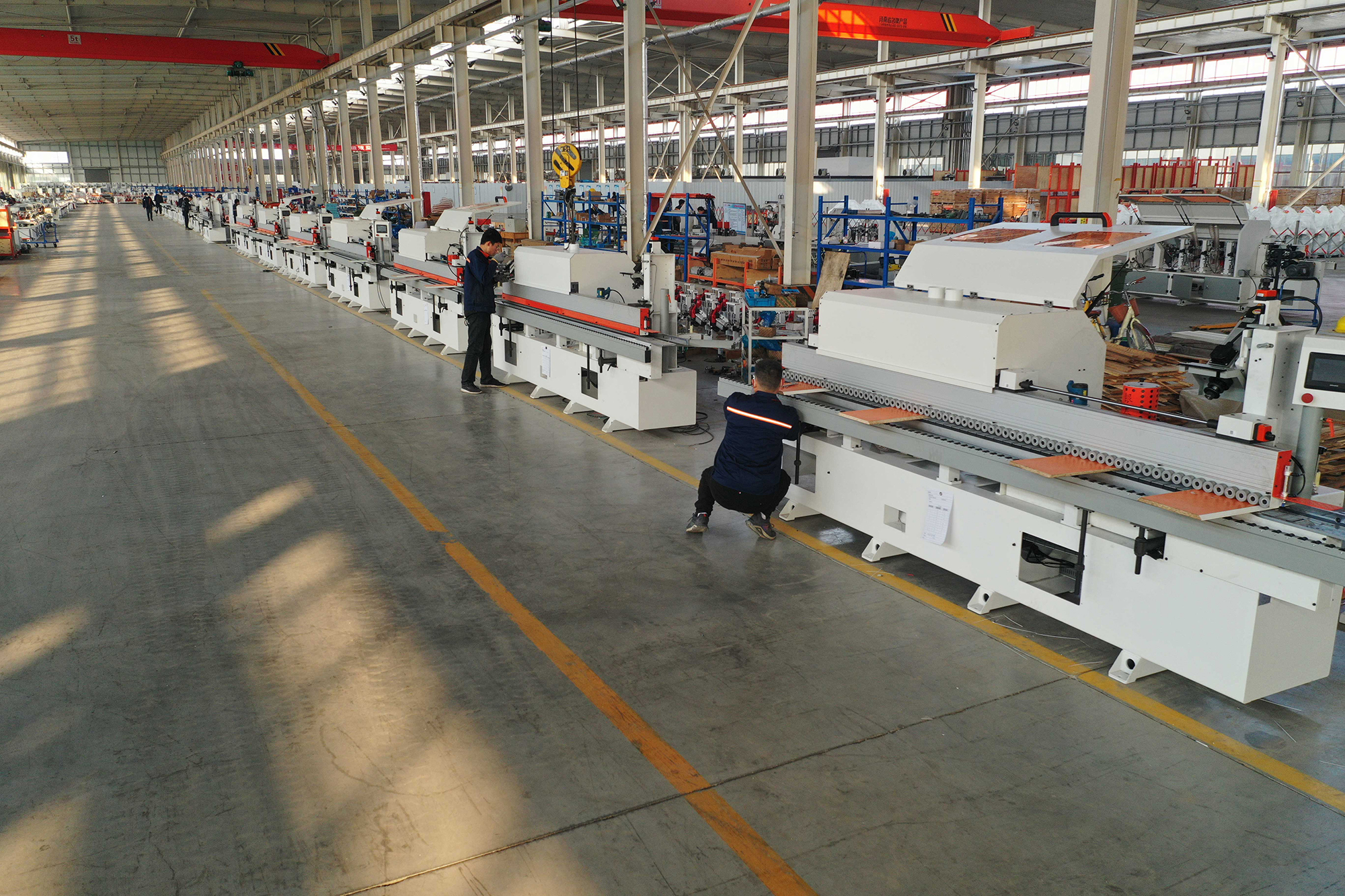
4. Choosing by Business Size and Needs
4.1. Small Workshops And Startups
For a small custom shop or startup, flexibility and budget are paramount.
Table saws or small sliding-table panel saws are common first machines. A portable circular saw or handheld jig saw can supplement for short runs or on-site work.
Desktop CNC routers (with 2–3 kW spindles) may suffice for prototype furniture parts. For very small volume, even a combination saw/router workstation could work.
4.2. Medium Enterprises
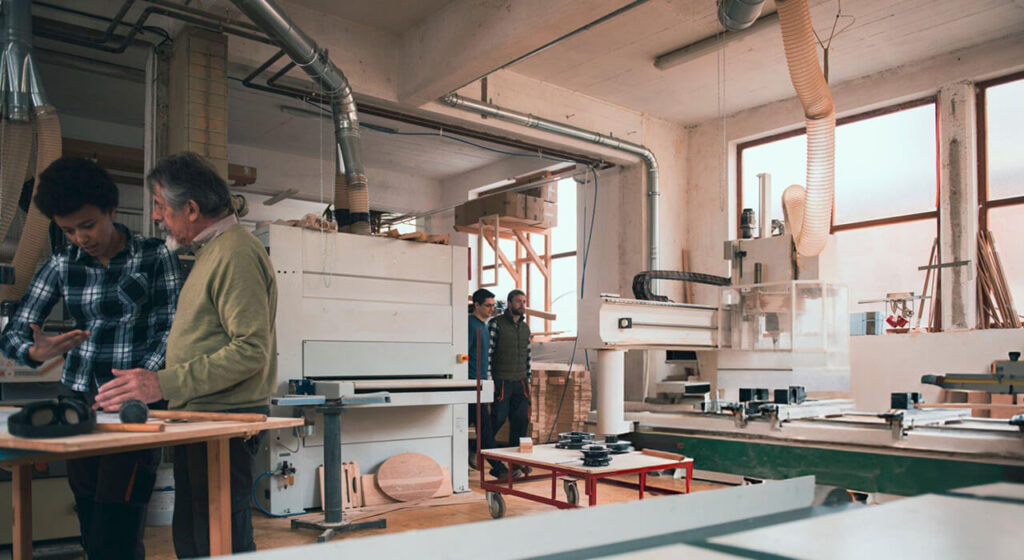
As production grows, a dedicated panel saw (sliding table) or semi-automatic CNC router often becomes necessary.
Shops making hundreds of panels weekly will benefit from a mid-range CNC router (with nesting software) or a panel saw with power-feeds.
A 5-axis CNC may be overkill, but a 3-axis CNC with automatic tool change can improve throughput. Medium shops also start to use dust collection systems and might invest in laser cutting if intricate parts are common (e.g. decorative inlays).
4.3. Large Furniture Manufactures
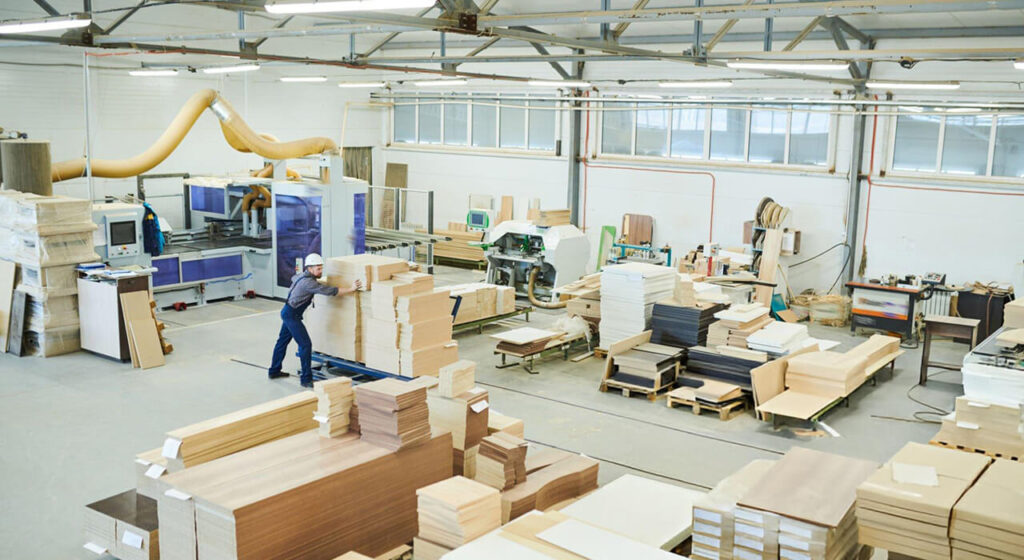
High-volume factories should invest in fully automated cutting centers.
Typical solutions include beam saws (large horizontal panel saws) and multiple CNC routing stations. Nesting-based CNC production lines allow the best material usage and minimal labor.
For example, a factory might have a large gantry router with automatic sheet feeder and stacker, cutting dozens of parts from 4×8′ sheets with minimal operator input.
Beam saws can cut several sheets per minute with pneumatic sheet lifts and automatic scoring. In some cases, robotics unload finished parts.
Budget is higher at this scale, but productivity gains (and waste reduction) justify it. Always align machine capacity with your daily production volume and part complexity.
5. Pros and Cons of Different Technologies
Different cutting methods have trade-offs. In summary:
5.1. Panel/Sliding Table Saw
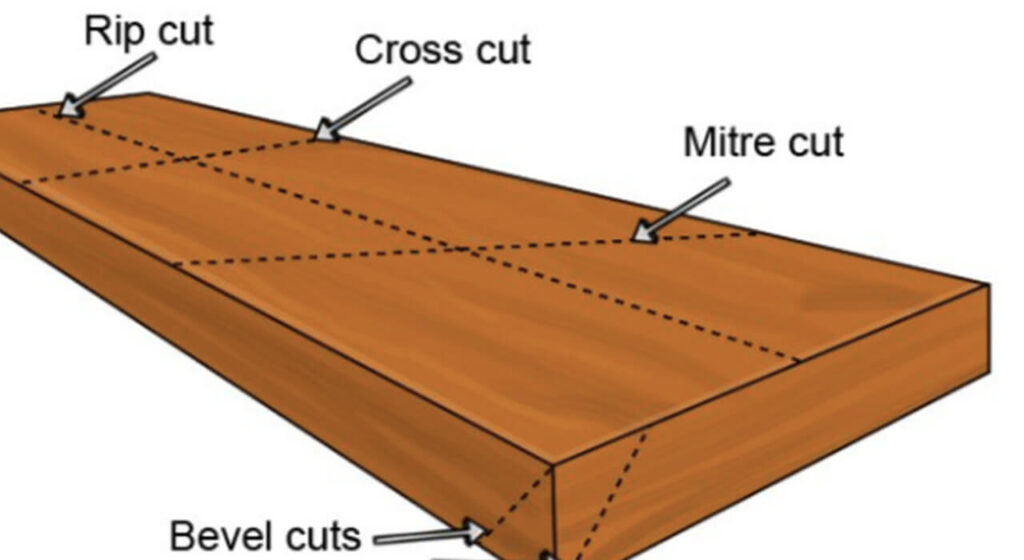
Pros: Fast, robust cutting of large panels with straight cuts; relatively low cost per square foot cut; simple to operate. High feed rates make them ideal for bulk ripping or cross-cutting panels.
- Cons: Only cuts straight lines and angles; no capability for holes or internal contours without manual jigs. Require manual or powered sheet handling. Not suitable for curved cuts or complex shapes.
5.2. CNC Router
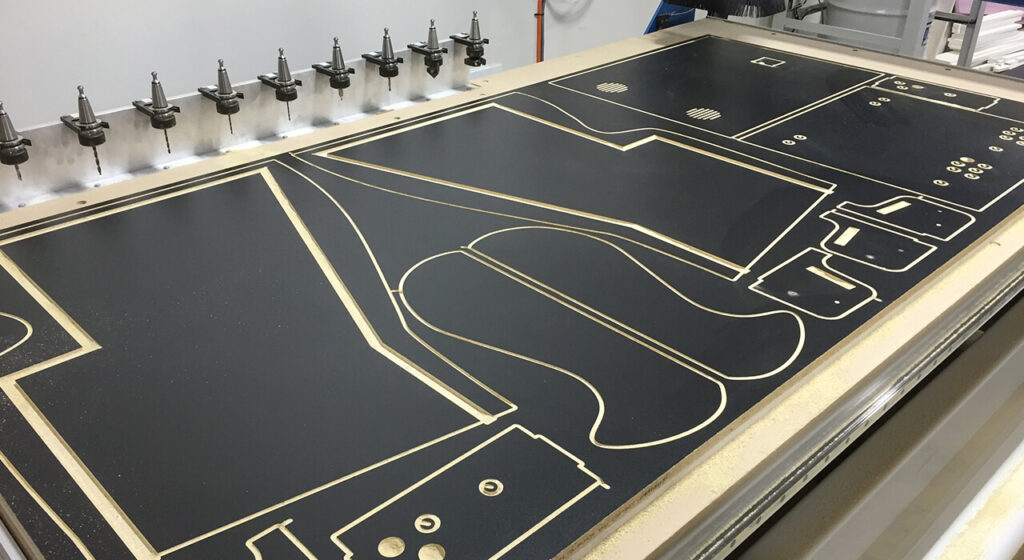
- Pros: Extremely versatile – can cut any 2D contour (and some 3D relief). Automating complex patterns saves labor. Good for nesting to minimize waste. Generally lower capital cost than lasers for large tables. CNCs can also drill and tap. As one industry guide notes, CNC machining is “relatively low-cost” and energy-efficient compared to lasers.
- Cons: Mechanical wear (bits wear out). Still slower than a saw for a simple straight cut. Requires training/programming. Larger footprint.
5.3. Laser Cutter
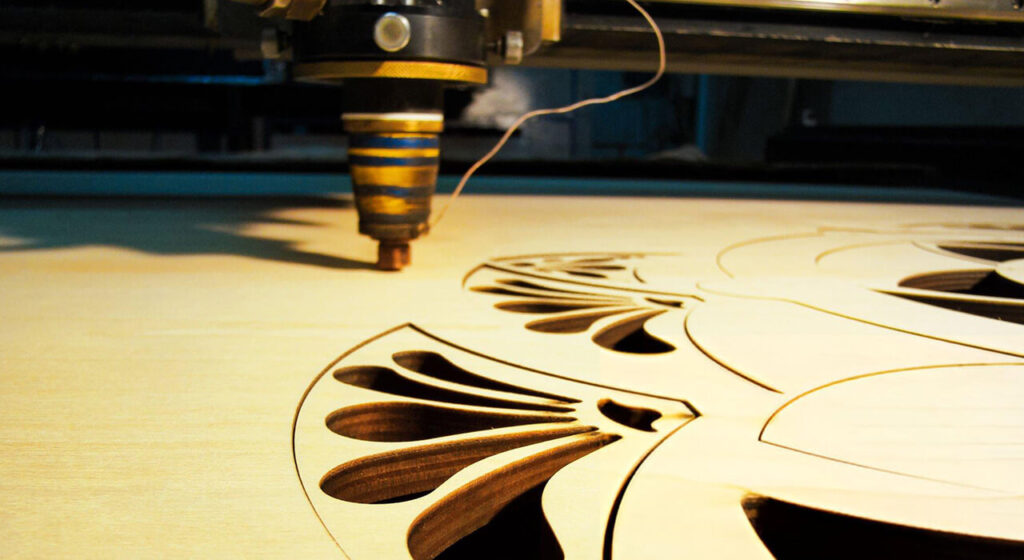
Pros: Unmatched precision and detail (kerf <0.1 mm). Laser edges are sealed (burned), which can prevent delamination or fraying. Excellent for complex inlays, furniture accents, and engraving graphics. Little vibration or mechanical force. Can cut (and engrave) many materials, not just wood. As Plyco observes, lasers offer fineness that “just isn’t possible through friction-based” cutting.
Cons: High initial cost (machine and optics) and operating cost (electricity). Limited cutting thickness (typically up to ~12 mm in one pass for plywood). Some plywood glues are hazardous under laser. Require fume extraction. Slower at thick sections (may need multiple passes).
5.4. Table Saw
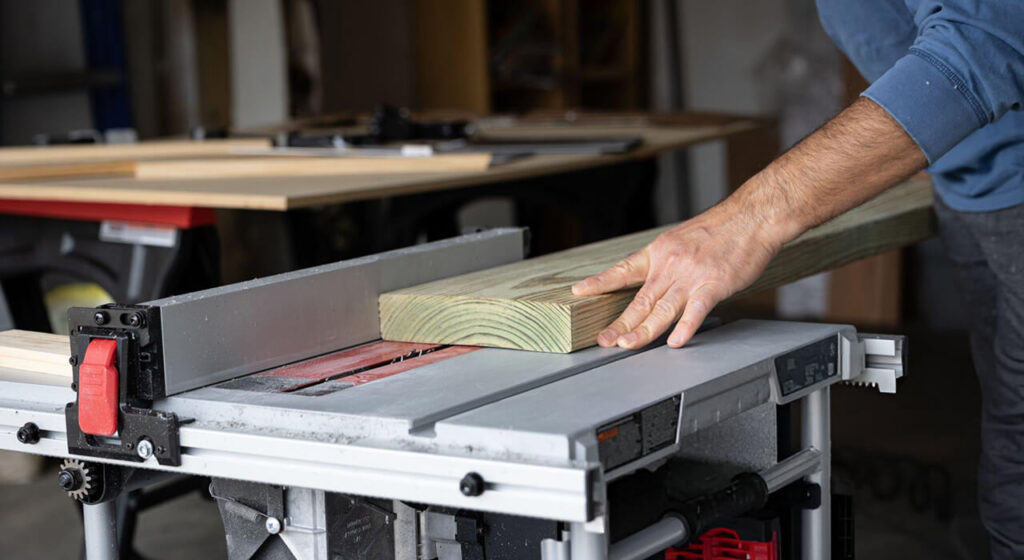
Pros: Versatile and familiar. Table saws can make most straight cuts needed in furniture parts (crosscuts, rip cuts, miters). Low cost and simple operation for moderate volume. Accessories (tenoning jigs, dado blades) add functionality.
Cons: Lower capacity (table size and blade height) than panel saws. Dangerous if guards/safety features are not used. Less repeatable for production.
5.5. Handhold Saw
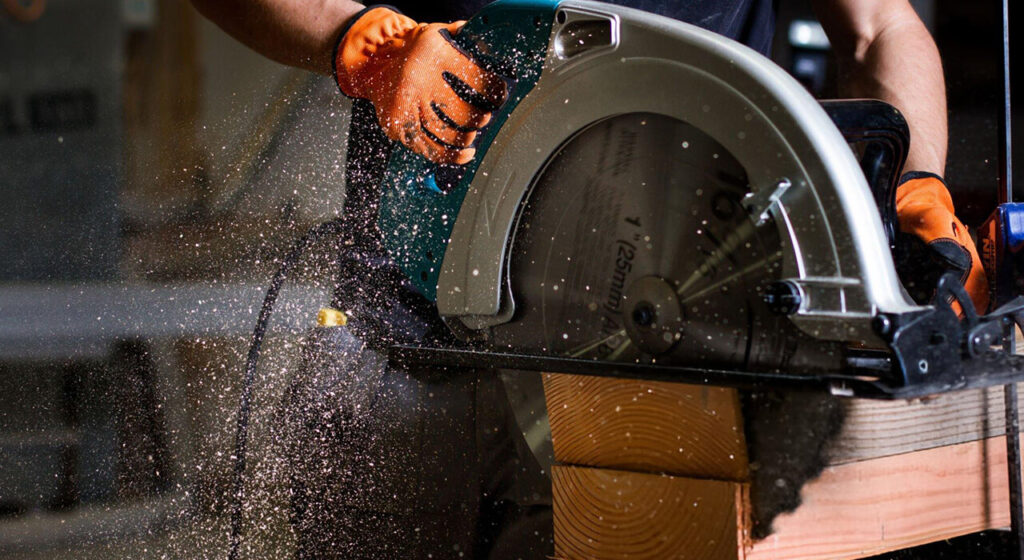
- Pros: Extremely flexible for on-site or one-off cuts, curves, and special angles. Portable and low cost.
- Cons: Poor precision and consistency. Not suited for batch production.
In essence, if you need speed and volume with simple shapes, panel saws or CNC nesters excel. If you need extreme precision and detail, lasers or high-end CNC routers are better. Each technology’s strengths come with corresponding limitations, so a shop often uses a combination of machines.
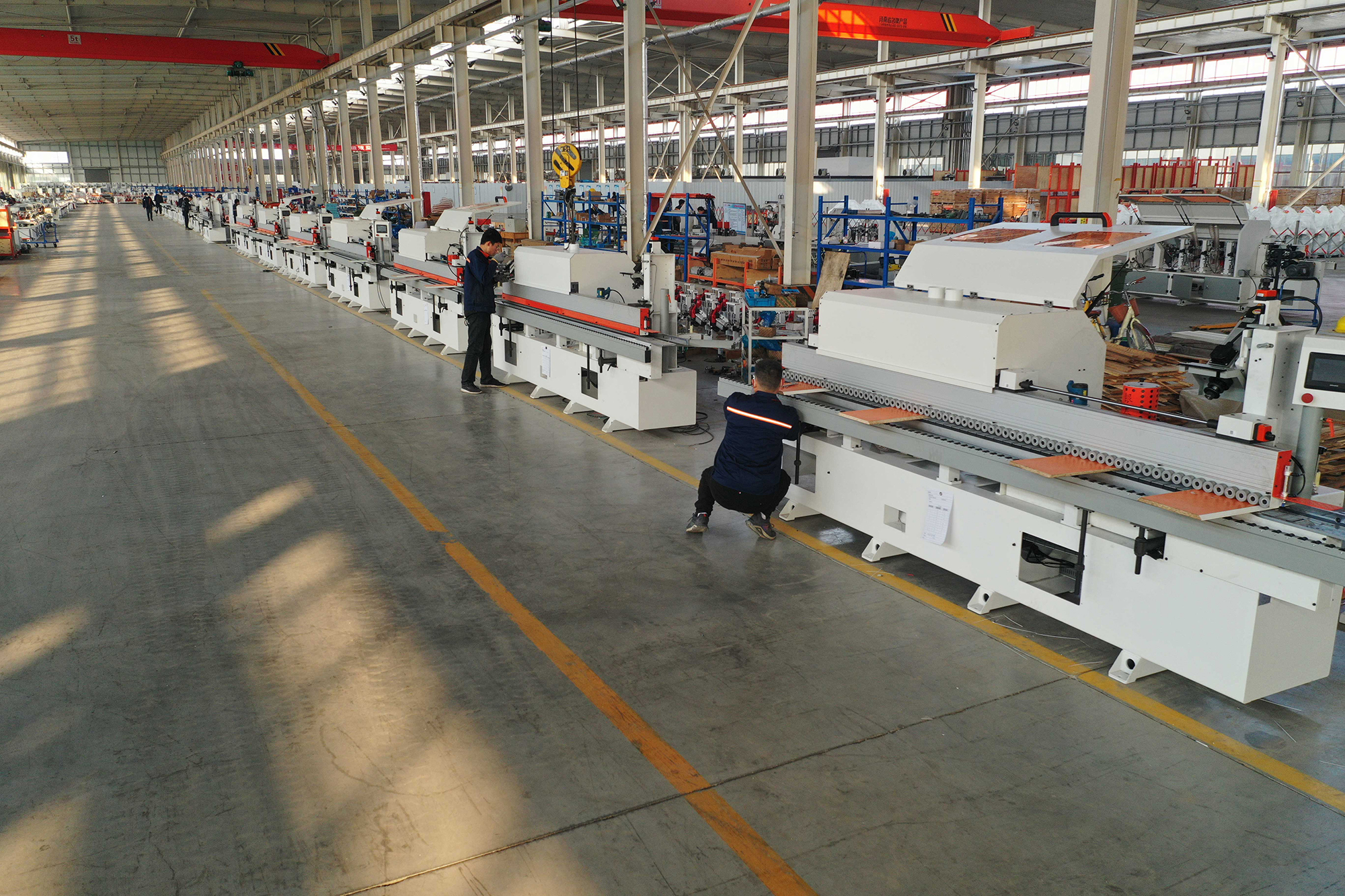
6. Common Mistakes to Avoid
When purchasing, beware of these pitfalls:
-
Mismatched Capacity: Don’t buy “too small or too big”. A common error is underestimating the plywood size or volume needed. Too small a machine will hamper production; too large will waste space and budget. Always honestly assess the largest sheet size and daily quantity you will cut.
-
One-Size-Fits-All Expectation: No single machine does everything. As Popular Woodworking warns, “expecting one machine to do the job of many is folly”. For instance, a panel saw cannot cut internal cutouts or engrave, while a laser cannot rip thick boards. Plan for a combination of machines (e.g. a panel saw for straight cuts plus a CNC router for details) if your product mix is diverse.
-
Overlooking Ongoing Costs: Focusing only on purchase price is risky. Remember consumables (blades, bits), maintenance, and power usage. For example, laser cutters consume significant electricity and the CO₂ tube has a limited lifespan. CNC routers need router bits, vacuum pumps, and lubricants. Factor these into your budget to avoid surprise costs.
-
Neglecting Dust and Environment: Cutting plywood generates a lot of dust. A mistake is not planning for proper dust collection and ventilation. Clogged filters or excess sawdust can damage machines and harm health. Ensure your buying plan includes dust extractors and spare filters.
-
Insufficient Training and Support: Even the best machine is ineffective without trained operators. Avoid buying a high-tech machine without training plans. Also, don’t skip on checking the vendor’s service network. Good after-sales support is crucial to minimize downtime.
-
Ignoring Safety: Never purchase a machine ignoring safety features to save money. Lack of guards, emergency stops, or dust extraction can lead to accidents and fines. Always verify that the machine meets industry safety standards before buying.
By steering clear of these errors, you’ll choose a machine that truly fits your operation.
7. Maintenance and Operation Tips
Proper upkeep is essential for long-term performance:
-
Regular Cleaning: Remove sawdust and debris daily, especially from moving parts. Clear dust from the table, rails, screw drives, and the cabinet interior. Clogged dust can increase wear and lead to misfeeds. (If the machine has a vacuum or compressor, empty it regularly.)
-
Lubrication: Keep guide rails, ball screws, and bearings well-lubricated. As one CNC maintenance guide notes, failure to clean and lubricate daily can cause increased friction, step errors, and wear. For manual lubrication machines, apply recommended oil every few days. Some CNCs have automatic oilers – ensure their reservoirs are filled.
-
Electrical Safety: Power off and lock-out the machine before maintenance. Check wiring and connections periodically. Be sure to keep the electrical box dry and dust-free; accumulate dust in the electrical cabinet can cause shorts or signal errors. Replace any damaged cables or outlets immediately.
-
Blade and Tool Care: Use sharp, appropriate blades and bits for plywood. Dull tools cut poorly and strain motors. For saws, choose the right tooth count and grind (e.g. ATB for plywood). For CNC routers, use carbide bits rated for wood. Rotate tools between shifts if needed, and inspect them for chips or cracks.
-
Coolant and Spindle (if applicable): For water-cooled spindles, keep the coolant clean and at proper level. Replace coolant regularly to avoid algae or sediment. Ensure no leaks in the water lines. Overheating a spindle will ruin bearings, so monitor the spindle temperature during long runs.
-
Calibration and Alignment: Periodically check that fences and stops are square and that linear scales are aligned. Recalibrate the machine (squaring the table to blade or beam) if you notice accuracy drift. Follow the manufacturer’s maintenance schedule for replacing belts, bearings, or filters.
-
Environmental Control: Wood dust and moisture are enemies of machinery. Do not expose the machine to rain or outdoor humidity. Install the machine on a solid, level floor. Sudden power surges can damage electronics, so use a stable power supply; ensure the voltage matches the machine’s requirements.
-
Operator Training: Finally, enforce proper operating procedures. Train all users on safe handling, correct speeds/feeds, and emergency shutdown. As StyleCNC emphasizes, operators should follow company training rules and not exceed the machine’s specs. A well-trained operator will catch issues early and prolong machine life.
Regular preventive maintenance (cleaning, lubricating, checking) will greatly extend the life of your cutting equipment and keep it running safely and efficiently.
8. Final Decision Checklist
Before you buy, run through this quick checklist to ensure a good fit:
-
Define Your Needs: Sheet size, thickness, and daily production volume required.
-
Match Machine Type: Do you need straight cuts only, or also curves and pockets? (Choose panel saw, CNC, or laser accordingly.)
-
Evaluate Features: Does it have the feed rate, precision, and automation features your shop needs?
-
Budget and ROI: Compare machine prices and calculate payback time (consider labor savings and waste reduction).
-
Space and Utilities: Ensure you have room and the necessary power/dust-collection infrastructure.
-
Safety and Support: Verify safety guards, emergency stops, and vendor service options.
-
Warranty and Service: Check warranty coverage and proximity of tech support.
-
Operator Training: Plan for getting operators trained before startup.
By carefully considering these factors and using the insights above, you can confidently select the plywood cutting machine that best suits your furniture manufacturing or woodworking operation.